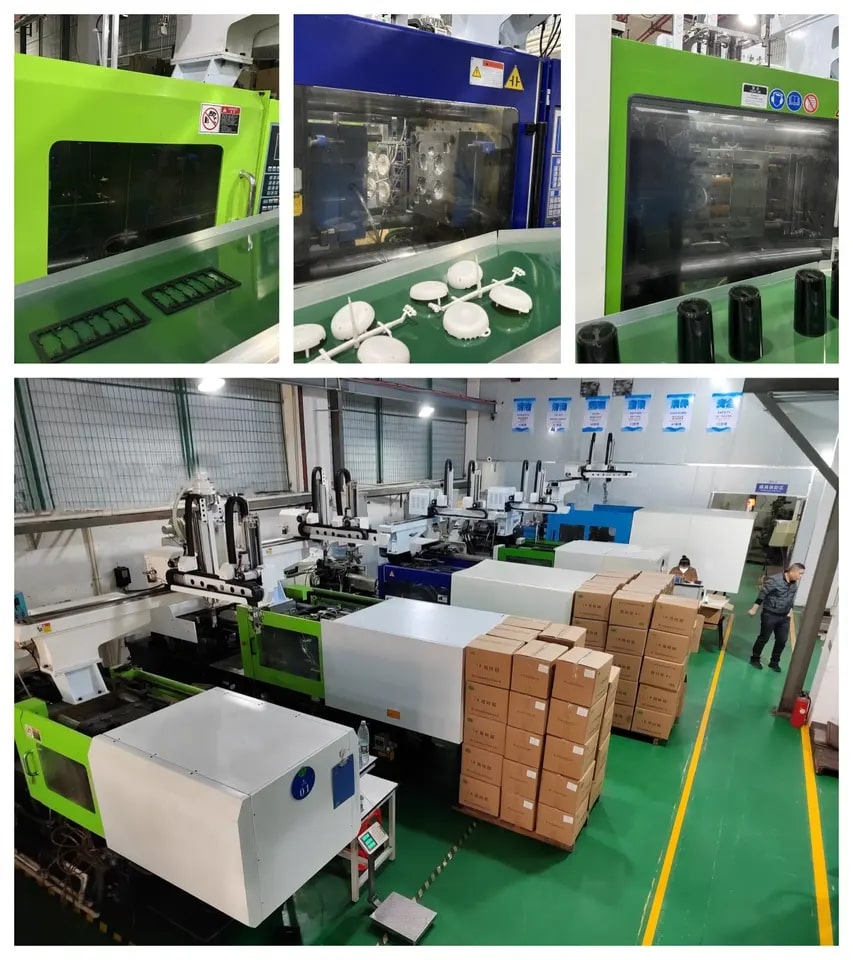
You may already know how phone cases are made, but you must not be aware of the important tools used in the production of phone cases — at the heart of the process of phone case manufacturing is the creation of the molds that shape the final product. So next, let’s examine why mold making for phone cases is so important and explore the techniques, materials, and processes involved.
8 Sections Tell You Why Phone Case Mold Is Vital
1: Understanding Phone Case Manufacturing
Phone cases have become a ubiquitous accessory, reflecting users’ personalities and safeguarding their devices. To meet diverse customer preferences, manufacturers rely on an array of materials like TPU, PC, and silicone, each offering unique properties suited for various phone case designs.
2: The Significance of Molds in Phone Case Production
Molds are the unsung heroes of phone case manufacturing, enabling mass production with precision and efficiency. By using molds, manufacturers can ensure that every case maintains consistent dimensions, fit, and functionality.
3: Design and Prototyping of Phone Case Molds
Creating a phone case mold begins with a meticulous design using advanced computer-aided design (CAD) software. Iterative prototyping is crucial to refining the mold’s design, identifying potential issues, and achieving the desired end product.
4: Manufacturing Techniques for Phone Case Molds
Phone case molds are crafted using various manufacturing techniques. Injection molding, the most prevalent method, offers high-speed production with minimal material waste. Additionally, compression molding and 3D printing find applications in specific scenarios, each with its merits and limitations.
5: Materials for Crafting Phone Case Molds
The choice of materials used in mold making significantly impacts the mold’s durability and lifespan. Commonly, molds are made from aluminum, steel, or silicone, each selected based on factors like production volume, complexity, and budget considerations.
6: The Process of Mold Production
The process of making a phone case mold requires precision engineering and state-of-the-art technology. CNC machines play a crucial role in manufacturing molds, ensuring accuracy and consistency throughout the production process.
7: Quality Control and Assurance
Maintaining strict quality control is essential to ensure the integrity of phone case molds. Techniques like mold flow analysis are employed to optimize mold design, minimize defects, and improve production efficiency.
8: The Cost Considerations of Phone Case Mold Making
The expense of phone case molds is influenced by multiple factors. Advanced technologies, high-quality materials, customization needs, low-volume production, and ongoing research and development contribute to the overall cost.
In a Word
Phone case mold making is a critical step in delivering durable and appealing accessories to consumers worldwide. The intricate blend of technology, craftsmanship, and material selection ensures that manufacturers can produce a wide range of phone cases to suit individual preferences and protect devices effectively.
Moreover, if you are a small brand side of the phone case and don’t have enough money, you can also buy a certain phone case model from a first-class manufacturer and then look for a cheaper production workshop to cooperate with, of course, due to the high cost of the molds then the charge for this independent service is certainly not cheap. Why are molds so expensive?
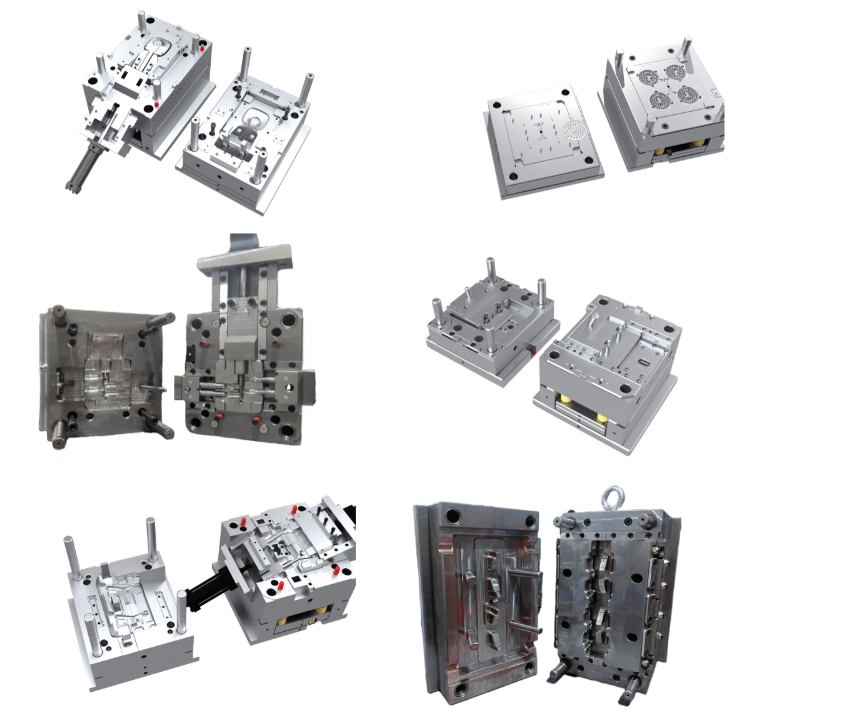
Why Phone Case Molds Are So Expensive?
Creating the molds that give them phone case form and functionality. While phone case molds play a pivotal role in mass production, their high cost may raise questions. So why are the technical reasons behind the expense of phone case molds and gain insight into the complexities of their manufacturing?
7 Reasons Proved Why Phone Case Molds Expensive
1. Precision Engineering and Technology
Phone case molds demand a level of precision engineering that ensures each case is flawlessly replicated. Advanced technologies like computer-aided design (CAD) software and high-precision CNC machines are employed to create intricate mold designs and achieve consistent dimensions. These cutting-edge tools contribute significantly to the overall expense of mold making. According to industry research, CNC machining for mold production can cost anywhere between $2,000 to $30,000 per mold, depending on the complexity of the design and the material used.
2. High-Quality Materials
Durability and reliability are paramount when it comes to phone case molds. Using top-grade materials such as high-quality aluminum or steel ensures the molds can withstand the rigorous demands of mass production. These premium materials, though costly, are essential to prevent mold deformation, corrosion, and wear, extending the mold’s lifespan. Premium mold materials, such as hardened steel, can contribute up to 50% of the total mold-making cost, making material selection a critical factor in the overall expense.
3. Customization and Complexity
Phone cases today are more than generic designs; they often feature intricate details and personalized elements. Customizing molds for each unique design adds complexity to the manufacturing process, driving up costs. The need for precise customization and attention to detail necessitates additional efforts during mold design and production. A study by a leading mold manufacturer revealed that customized molds account for approximately 30% higher production costs compared to standard molds used for basic phone case designs.
4. Rigorous Testing and Quality Assurance
Ensuring the utmost quality and reliability of phone case molds requires extensive testing and quality assurance procedures. Mold flow analysis, simulation tests, and stringent quality checks are conducted to identify potential flaws and optimize the mold design. These meticulous tests contribute to the overall cost of mold making but are essential for producing high-quality phone cases. Mold flow analysis and simulation tests can account for an additional 10% to 15% of the total mold-making cost due to the specialized software and equipment required for these processes.
5. Low-Volume Production
Despite the high demand for phone cases, some designs or models may not have as significant sales volume. In such cases, the cost of mold production gets distributed across a smaller number of units, leading to higher costs per unit. Lower production volumes can impact the overall affordability of phone case molds. According to industry reports, low-volume production molds can cost 20% to 30% more per unit compared to molds used for high-volume phone case designs.
Research and Development
Phone case mold manufacturing is an ever-evolving field that requires continuous research and development. Investing in new technologies, exploring innovative materials, and refining manufacturing processes are ongoing efforts to improve mold quality and efficiency. These advancements contribute to the overall cost of mold making. Mold manufacturers allocate approximately 5% to 10% of their annual budget to research and development, reflecting the importance of innovation in mold-making processes.
7. Environmental and Regulatory Considerations
Adhering to environmental regulations and safety standards may lead to additional expenses in mold making. Eco-friendly manufacturing processes and compliance with stringent regulations ensure responsible production but may incur higher costs. Environmentally friendly mold-making practices can increase the overall cost by around 5% to 8%, considering the adoption of eco-friendly materials and waste management systems.
Conclusion
The costliness of phone case molds is a result of the technical intricacies involved in their manufacturing. Precision engineering, high-quality materials, customization, rigorous testing, and continuous research contribute to the final expense. While phone case molds may seem expensive, their role in delivering durable and well-designed phone cases remains indispensable in meeting the demands of modern manufacturers.